Saab:s test med SLS-printad lagning blev lyckad
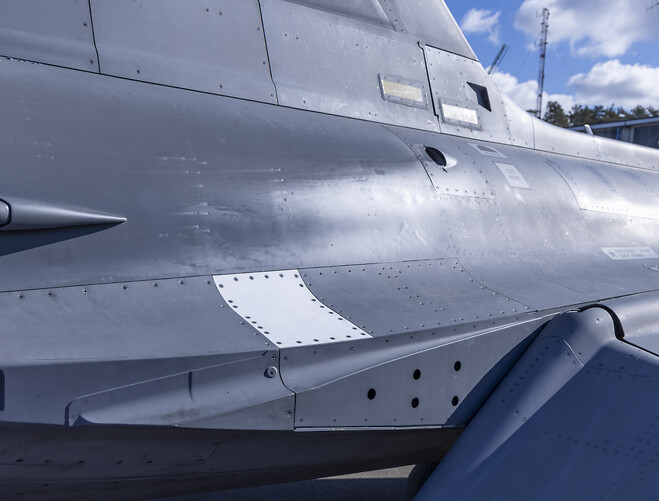
Vid strid är det svårt att förutse hur och vad som skulle kunna skadas på ett flygplan. Saab har därför initierat konceptet Battlefield damage repair som syftar till att kunna ta med produktionen till fältet via en 3D-skrivare, istället för att ta med alla möjliga reservdelar.
När det gäller flygplan är det dock extra viktigt att alla delar uppfyller höga standarder eftersom luftrummen utsätter flygplanen för tuffa krav. Därför såg Saab till att göra flera omfattande och noggranna prövningar innan planet testades i luften.
I testet användes en 3D-printad lucka som tillverkades av att originalluckan togs bort från flygplanet och placerades i en skanner. Denna process möjliggjorde i sin tur för en SLS-printer att göra en exakt kopia i materialet polyamid (PA2200), skräddarsytt för flygplanet.
– Potentialen med detta tillvägagångssätt innebär att underhållspersonal på fältet kan få tillgång till individuellt monterade reservdelar och att man inte längre behöver bryta ner andra flygplan för att hitta exakt rätt del, säger Håkan Stake, chef för utvecklingsprojektet på Saab.
Testflygningen ägde rum vid Saabs anläggning i Linköping och ansågs som en lyckad flygning.
– Den första inspektionen av luckan efter flygningen var mycket positiv och visade att inga visuella strukturella förändringar hade inträffat från flygningen, säger Håkan Stake.
I nästa steg kommer ytterliggare tester att genomföras. Samtidigt kommer Håkan Stahe och teamet på Saab att fortsätta att titta på alternativa material till PA2200, eftersom materialet som används i 3D-delarna behöver vara väldigt flexibla och tåla kyla i höga höjder.
– När det gäller att öka den operativa tillgängligheten på fältet kommer additiv tillverkning att vara en game-changer, säger Ellen Molin, vice vd och chef för Saabs affärsområde Support och service.